


SERVICES

Estimating
“Risk comes from not knowing what you're doing.”

Planning
“Even a correct decision is wrong when it was taken too late.”

Cost Control
“When you find yourself in a hole, stop digging.”

Procurement
“Better to have a simple model backed by excellent people than the other way around.”
What comes to your mind when you hear the term “Project Control”? Does taking control or authority over projects come to your mind?
Actually, in the world of project management, the term “control” has very little to do with dictating people what to do. The term “control” is similar to steering a ship.
It’s about continually making course adjustments with one main objective in mind: bringing the ship into safe harbour, as promised at the start of the journey.
How do you bring the ship to safe harbour? Well, by identifying a specific destination, carefully charting a path to get there, evaluating your location throughout the voyage, and keeping an eye on what lies ahead.
Our role at MineStone is like steering a ship to make sure it gets to the final destination on time and without extra cost. Another big role is “forecasting”. We always look ahead to foresee what is going to happen in your project so that you can take proactive or corrective actions required to bring your project back on track.

journey of project controls
The Project Controls Group usually is responsible for supporting project management, engineering, procurement, construction, and commissioning in formulating the planning and implementation of project controls, and for reporting on the project through all phases.
MineStone will implement, monitor, and report project performance against the project baseline schedule and budgets, and will participate in identifying variances from the baseline plans and forecasting potential impacts.
We will assist our clients with development of mitigation plans to reduce and eliminate the impacts of variances by integrating the following project controls functions:
PROJECT CONTROL CYCLE
- Project Scope & Definition
- Initial Planning & Development
- Capturing the Baseline
- Monitoring
- Performance Assessment
- Mitigation
- Budget Revisions & Forecasting
- Reporting
- Project Closeout
PROJECT CONTROL FUNCTIONS
- Support to Coding Structure
- Support to Initiation Planning
- Estimating
- Cost Control
- Planning & Scheduling
- Progress & Performance
- Trending & Forecasting
- Project Accounting
- Reporting
At the very early stages of the project development, MineStone get involve in setting project goals, identifying key milestones and appropriate relationships, and establishing priorities for the coordination of engineering, procurement/materials management, construction, and commissioning activities based on the contract.
During the planning phase, we will support each of the project disciplines to establish and implement the baseline schedule and control budgets in accordance with project procedures and instructions.
Elements of initial planning must include careful consideration of the following:
-
Contract requirements;
-
Critical design activities and interfaces;
-
Key drawings and deliverables;
-
Critical tie-in requirements (process and services);
-
Placement of POs for long-term-delivery items;
-
Major milestones for material take-offs, purchase fabrication, delivery to site, and installation;
-
Critical supplier design information (vendor data);
-
Field mobilization, and permitting or access constraints;
-
Project contracting strategy;
-
Definition and award of major construction contracts;
-
Mechanical completion, pre-commissioning, and start-up sequences for major process systems;
-
Project information turnover requirement.
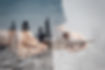
The client must ensure that the following information as a minimum is available and provided to the MineStone team in order to enable realistic planning of all phases of the project:
Engineering:
List of deliverables and estimated durations, sequence, and logic for production and issue
Procurement:
List of contracts, subcontracts, and purchases approved for the project (procurement and contracting strategy) and the delivery periods for major equipment and materials
Construction:
Methodology, sequence, and durations for construction activities
Commissioning:
List of systems, sequence, and durations for commissioning activities
Planning & Scheduling
The overall planning and scheduling process can be represented in two major stages:
-
Project Planning and Schedule Development, resulting in the formation of a Baseline Schedule
-
Schedule Management, Monitoring, Analysis, Reporting, and Mitigation, resulting in regular periodic schedule updates
The planning process will use a top-down approach for schedule development and a bottom-up approach for schedule management. The three levels of schedule hierarchy are outlined below.
Level 1 – Management Summary Schedule
The Level 1 Schedule provides a high-level management summary of the project. It will represent all phases, major areas, and key project milestones.
Level 2 – Project Master Schedule
The Level 2 Schedule will be used by the project leadership team as a strategic management schedule. It will represent major project components and their inter-relationships. It will also represent key control milestones that must be controlled via the trending process.
This schedule will typically contain no more than 200 activities.
Level 3 – Engineering/Procurement/Construction Control Schedule
The Level 3 Schedule is the detailed control schedule containing full Critical Path Method (CPM) logic and resource loading. The following are some key features of the Level 3 Schedule:
-
Represents the scope and execution strategies for EWPs, Procurement and Contract Packages, off-site fabrication packages (modules), CWPs, and Pre-commissioning and Commissioning system packages;
-
Presents a clear understanding of the project scope of work in alignment with the PCS;
-
Is pivotal to creating and validating all other project schedules, and rolls up into Level 2 and Level 1;
-
Shows control dates and interface milestones for special consultants and major contractors to provide clear linkage to their schedules;
-
Contains an adequate number of activities with realistic activity durations to clearly show the sequence and logic in performing the project in a systematic manner;
-
Defines the project critical paths and activity free and total floats;
-
Is fully resource-loaded to validate work force and peak requirements and address forecast requirements; this will realize optimum resource and funding utilization;
-
Is used to coordinate and control all activities on the project, and to perform critical path analyses and “what-if” schedules.
Once we the baseline schedule is freezed, the schedule will be regularly updated, at least monthly, providing the basis for status reporting, change forecasting, and controlling the project.
Organization charts, office staffing plans and histograms, and site work force histograms will be developed in alignment with the original approved baseline. These will be maintained and updated with actual data and forecast to complete.
Office staffing and site work force counts will be converted to equivalent hours by discipline and compared to the forecast hours to complete from the progress and performance reporting.
If the variance becomes too great, then a recovery plan will be generated.
These resource plans will be managed in alignment with the project approved hours as trended.

Estimating
At the beginning of every estimate we prepare an estimate execution plan that serves as the precursor to the formal basis of estimate. The plan details the following but not limited to:
-
Scope of the estimate, including schedule, matrix of responsibility, estimate platform and reference documentation;
-
Work breakdown structure;
-
The plan for direct costs, including level of MTO development, unit quantity preparation and deign growth / waste factors for all disciplines;
-
Equipment and material pricing and procurement strategy;
-
Labour rates; crew mixes, construction equipment and labour productivities;
-
Basis for field indirect and other costs.

This matrix and guideline provide an estimate classification system that is specific to the process industries.
Table 1 illustrates typical accuracy ranges that are associated with the process industries. Depending on the technical and project deliverables (and other variables) associated with each estimate, the accuracy range for any particular estimate is expected to fall into the ranges identified.
The Basis of Estimate (BoE)
We will prepare the capital cost estimate in sufficient detail to support the required level of accuracy for studies. Contingency will be applied to the base estimate corresponding to the risk analysis projection for that level.
We will develop preliminary materials quantities for the facilities on the basis of our layout drawings and sketches. Our capital cost estimating methodology encompasses direct and indirect field costs as well as other cost items. Direct field costs include labour, material, and equipment directly involved in the construction of permanent facilities.
The estimate will be based on the agreed-to project execution plan so that it adequately reflects the most likely contracting and construction approach. At the beginning of the study we will review existing cost data, schedules and reports, and establish a work breakdown structure (WBS) to be used for detailed estimates and cost comparisons.
Estimate Development
The following will be used to develop the detailed cost estimate:
-
An approved Basis of Estimate;
-
A clear definition of the Scope of Work and Coding Structures;.
-
Project Schedule Key Milestone targets;
-
A suite of engineering drawings in sufficient detail to support the defined accuracy of the estimate;
-
Quantification (MTOs) for all engineering discipline elements;
-
Engineering Deliverables estimate supported by engineering team;
-
Current pricing data and schedule information from potential vendors based on an agreed procurement and contracting strategy;
-
Methodology for indirect costs;
-
Approved approach to allowances (design development), escalation, risks, contingencies, and Client costs.
Estimate Review and Implementation Phase
Any changes identified during the estimate reviews will be incorporated into the estimate. Further estimate updates and reviews will be held as necessary with the Client, Project Manager, Lead Estimator, Project Services Manager, and the Project Management. Results of the reviews will be documented while any changes agreed to by both the Project Team and the Client will be incorporated, and the estimate will be formally issued.

Key estimating services for the project will include:
-
Establish the Estimate Execution Plan;
-
Establish estimate input requirements;
-
Develop Coding Structure;
-
Develop the Directs & Indirects estimate;
-
Develop the Material Take Off (MTO), design growth and waste factor allowances;
-
Develop the contingency, risks, escalation and owner's cost
-
Lead the estimate reviews;
-
Assist the cost control group with the transition mapping of the approved estimate to establish the project cost control budget (baseline);
-
Provide ongoing estimates of work associated with project trending and change control;
-
The scope of estimating includes an estimate of the forecast final cost of the project; defines the scope, major assumptions, limitations, and exclusions; provides an indication of accuracy; and expands any preliminary estimates into a more detailed cost estimate.

Estimating services for the project will include:
-
Establish the Estimate Execution plan and input requirements;
-
Develop MTO, growth design, waste allowances and other factors;
-
Develop the estimate directs and indirects;
-
Develop the escalation, contingency, risks and owner costs;
-
Develop the basis of estimate and reporting;
-
Lead the estimate reviews;
-
Assist the cost control group with the transition mapping of the approved estimate to establish the project cost control budget (baseline);
-
Provide ongoing estimates of work associated with project trending and change control;
-
The scope of estimating includes an estimate of the forecast final cost of the project; defines the scope, major assumptions, limitations, and exclusions; provides an indication of accuracy; and expands any preliminary estimates into a more detailed cost estimate.
Cost Control
The scope of the cost control services including reporting and project calendars will be agreed with the Client at inception of the project. The major aspects of cost management would include:
-
Establishing a control baseline (budget);
-
Monitoring and tracking (committed, incurred);
-
Analyzing and forecasting (trending, forecasting);
-
Reporting;
-
Participating in the potential mitigation process;
-
Contingency controls.
Original Budget
The Original Budget is prepared by re-casting the cost data from the approved estimate. The cost elements are coded and grouped to reflect the project execution strategy, mapped to the Project Coding Structure, and loaded into the client tailor made cost system as the original budget.
This budget will need to be approved by the relevant Project Manager/Director as a base control budget. Approved changes to the budget will be allocated against the correct cost codes and a current approved budget will become the basis for cost control.
Commitment Cost
Commitments are the value of awarded contracts, Purchase Order's, service agreements, or any other agreement. They represent what the Client and contractor or vendor has agreed or committed to, in terms of the goods and services that are to be provided.
The value of commitments made during the project is defined as follows:
-
Lump sum items: face value of the contract, including approved change orders.
-
Unit price items: incurred cost of the item based on units completed.
-
Cost reimbursable items: total value of the contract.
Incurred Cost
Incurred costs are the contractual value of work completed at a specific time that can be invoiced. There is no consideration for cancellation costs if the project were to be cancelled.
Incurred costs are evaluated relative to a status or cut-off date, which is consistent with status dates set for progress measurement. Therefore, and for reasons of timeliness, it will be necessary to estimate a portion of the total cost incurred to match the Client’s period cut-off.
Various methods of incurring will be used depending on the commercial nature of the item. These are generally categorized below and addressed in more detail in the cost control system.
-
Reimbursable Engineering, Procurement, and Project Management;
-
Procured Items;
-
Reimbursable Direct and Indirect Labour Costs;
-
Lump Sum Contracts;
-
Owner’s Cost.
Invoicing and Payments
Generally invoicing is represented in two categories:
-
Invoices from us to the Client which credits our corporate accounts
-
Invoices received from Service Providers, Material Suppliers and Subcontractors
The process of invoicing and payments is managed by the project accounting group but is often an integrated effort with the cost control group, who can assist with validation and alignment with incurred. Regular, usually monthly, reconciliations between cost control and project accounts is essential.
Cost Forecasting
Going forward during the life of a project, additional factors may come into play such that the Forecast Final Cost (sometimes referred to as the Forecast at Completion) may either increase or decrease.
Forecasting of the project cost will be the result of monitoring work performed against the original budget, analyzing changes from the control base, and predicting to-go performance. The forecasting process will incorporate the change management and trending process as well as the independent application of analytical techniques and tools. As changes are identified through the analytical forecasting process, they will be input into the change management and trending processes.
The main methods adopted in our systems are as follows:
-
Forecast Final Cost as supported by Trends
-
Forecast Final Cost as supported by Forecast From Commitment
-
Forecast Final Cost as supported by statistical analyses based on Performance Factors (PF)
-
Forecast Final Cost based on revised detailed estimate
Project Change Control & Trending
The trend alert stage provides for quick and early warning of a potential project impact. A trend alert is presented to the Client with a brief description, rough order-of-magnitude cost, and schedule impact with appropriate supporting documentation. Client approval or rejection is required prior to further action.
If, and upon, Client approval of a trend alert, then we will proceed with the work in accordance with Client instruction provided. We will prepare a formal trend with appropriate level of cost estimate and schedule, properly coded in alignment with Project Coding Structure. This will allow for incorporation into the budgets and schedule for proper control of the scope addressed by the trend. The trend will be submitted for client approval. Client approval is required prior to our incorporation into the project controls. Upon approval, we will load the trend into the project controls tools.
We will assess any potential project impact of change and will raise a Change Order request for any trends or groups of trends only when contract criteria for Change Order are met.
Reporting
Monthly progress report will include KPI's that will be presented at a simplified management level as well as in more detailed reporting. These will be presented on a monthly basis, in both graphic and tabular format, and will be at an appropriate level of detail to capture a summary of the key aspects.
These KPI's and reporting will include the following:
Schedule
- Project Control Milestones
- Progress (% complete)
- Baseline vs. Actual vs. Forecast to Complete
Cost
- Baseline vs. Current Budget vs. Current Forecast Final
- Cost Flow of Original Baseline vs. Actual vs. Forecast to Complete
Change Control and Trending
- Number of Trend Alerts, Approved, Rejected & Cancelled
- To date and current month
(EPCM) Staffing
- Baseline vs. Actual (equivalent) vs. Forecast to Complete
- Headcount
- Unfilled positions
Key Engineering Deliverable Counts
- Key Engineering Deliverable Counts
- PFD's, P&ID's, Isometrics (ISOs), Electrical Single Lines, Loop Drawing